In the realm of custom metal dome keypads, two primary manufacturing methods have emerged: laser etching and mold production. While both techniques result in quality products, they possess distinct differences that cater to varying requirements. In this article, we’ll delve into these methods and shed light on the crucial parameters and performance aspects of metal dome keypads.
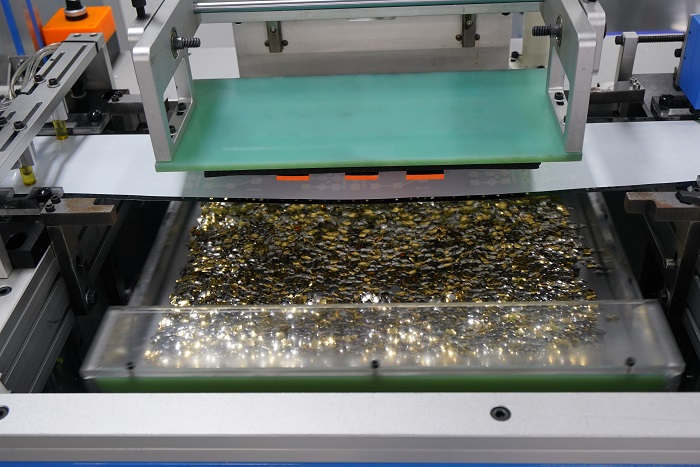
1. Manufacturing Methods: Laser Etching vs. Mold Production
Metal dome keypads can be crafted using either laser etching or mold production, each with its own set of advantages and considerations.
Laser Etching:
Laser etching is well-suited for applications where precise dimensions and intricate designs are paramount. The maximum size achievable through laser etching generally remains under 100mm. This method offers exceptional precision, with dimensional inaccuracies typically falling within the range of 0.25mm to 0.3mm. Laser etching is especially popular for designs that require fine detailing and relatively lower production quantities.
Mold Production:
In contrast, mold production offers greater flexibility in terms of size and dimension. The molds can yield metal dome keypads with dimensions that far exceed the limits of laser etching. Additionally, mold-produced keypads exhibit tighter precision, with dimensional errors often confined to 0.15mm or less. This method is favored for applications demanding high precision and larger production volumes.
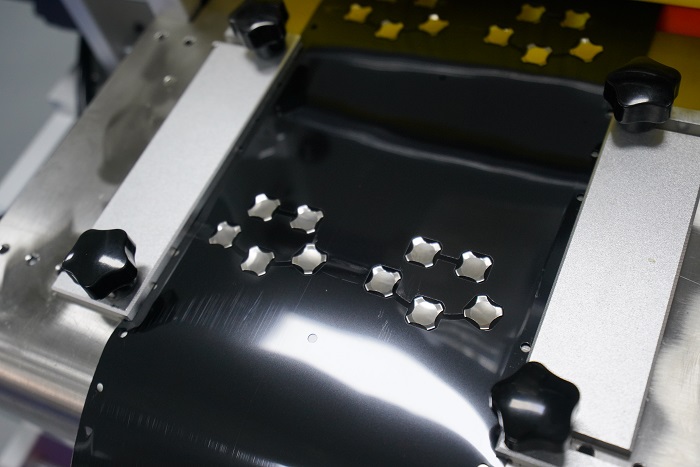
2. Essential Parameters for Designing Custom Metal Dome Keypads
When designing and manufacturing a custom metal dome, several key parameters must be considered to ensure optimum performance and compatibility with the intended application. Prevents problems when the metal dome is installed on the keyboard.
Key Parameters to Consider:
Button Placement: Clearly indicate the central location of each button, as this aligns with the center point of the metal dome placement.
Mechanical Hole Locations: Accurately mark the positions of mechanical holes, such as those needed for LEDs, positioning, and soldering points. This prevents interference with essential components.
Overall Product Shape: The exterior shape of the keypad should harmonize with the outline of the PCB board.
EMI Shielding, Adhesive, and Light Guide Film: Specify whether EMI shielding, double-sided adhesive, or light guide films are required for the design.
Metal Dome Specifications: Define the specifications for the metal dome, including shape, diameter, force sensitivity, and material composition.
Tolerance Requirements: Establish tolerance requirements for various aspects, such as dimensional tolerances and the tolerances between buttons.
In conclusion, the choice between laser etching and mold production for crafting metal dome keypads hinges on factors like precision, size, and production volume. While laser etching excels in intricate designs and moderate volumes, mold production offers versatility in size and superior precision, particularly for high-volume applications. When designing custom metal dome keypads, careful consideration of key parameters ensures a product that meets the highest standards of performance and quality.